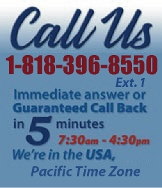 |
|
|
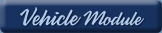 |
|
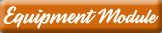
|
|
|
|
|
|
|
|
|
|
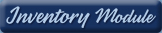 |
|
EZ Maintenance WEB™ |
|
Our Web version of EZ
Maintenance™, EZM Web™
is accessible anywhere in the
world there is an internet
connection.
|
|
 |
Partial Client List |
|
EZ Maintenance™ for Windows
|
EZ Maintenance™ for Web |
|
|
|
Features |
|
- Schedule All Maintenance
- Equipment & Vehicles
- Full Inventory Control
- P.O.s, RFBs, Invoices
- Work Orders, Bar Coding
- Emergency Work Orders
- Email Alerts
- QuickBooks Link
- Send Work To Vendors
- Customer/Vendor Tracking
- Track Customers
- Maintenance Histories
- Access Passwords
- Supervisory Control
- And Much More!
|
|
Contact Information |
|
Pinacia Inc.
5699 Kanan Road, #349
Agoura Hills, CA USA 91301
Phone: (818) 396-8550
Sales Support: ext. 1
Tech Support: ext. 2
Fax: (818) 396-3524
info@pinacia.com
|
|
|
|
 |
Previous
Section:
Viewing Maintenance
Due |
Next
Section:
Maintenance Due Report |
Watch a Video on Viewing and Entering Your Equipment in EZ Maintenance.
Creating Scheduled and Unscheduled Work Orders
First we'll show you how scheduled work orders are created in EZ Maintenance
software, and after that we'll show you how unscheduled work orders are
created.
To create a work order for a preventive maintenance event (a scheduled work
order) for a piece of equipment in EZ Maintenance, you simply select the
scheduled maintenance event which you want to create a work order for and
click on the Create/Edit Work Order button in the window
seen below. In this window, you can see all of the scheduled maintenance
events for a selected piece of equipment.
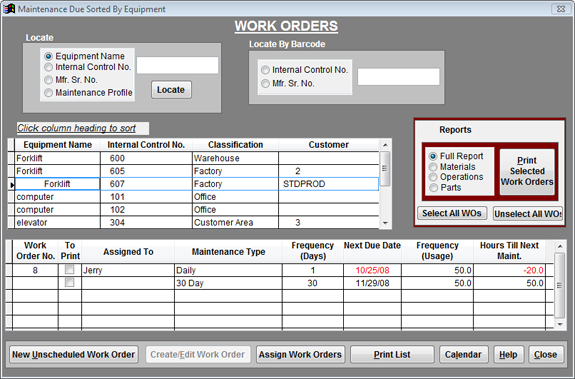
In the above window you'll see two lists: the top list contains the list of
equipment which you've entered into EZ Maintenance for tracking:
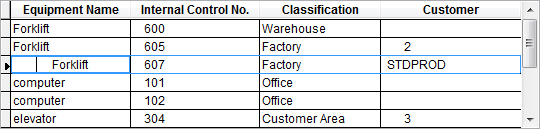
If you click on a piece of equipment in this list, the list of scheduled
preventive maintenance events, which is directly below, will be updated with
the scheduled maintenance events for that piece of equipment:

One of the scheduled maintenance events in the above example has had a work
order created for it. This is indicated by the number "8" under the Work
Order No. column, which is the number for the work order that
was created. In addition, the due date for the preventive maintenance event
is displayed in red, which means that
it is overdue. The person to whom each work order is assigned is also
displayed under the Assigned To column; the work order
number 8 is assigned to "Jerry".
As mentioned above, if you want to create a new work order, just select a
maintenance event that hasn't had a work order created for it and then click
on the Create/Edit Work Order button. This opens the
following window where you enter the information for the work
order:
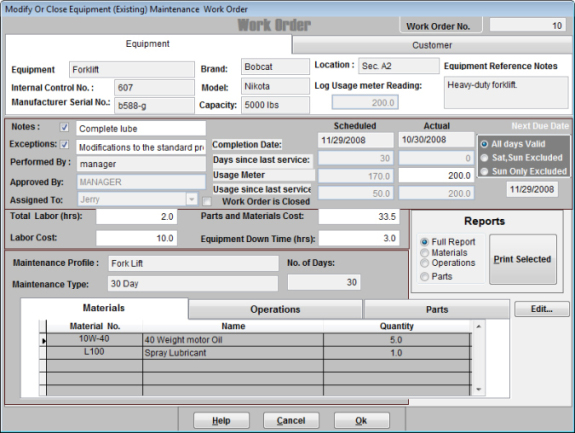
This window contains all of the details about the work order including:
- Details for the equipment you're creating the work
order for
- The customer who you're maintaining the equipment
for (if you are maintaining it for somebody else)
- What kind of maintenance the work order prescribes
(e.g. "quarterly maintenance", "daily maintenance", etc.)
- Any notes you want to add to the work order and
who is performing the work, who the responsibility for
completing it is assigned to, and who has
approved it
- The labor cost, materials/parts cost, and down
time necessary while the maintenance is being performed
- The materials and replacement
parts used in the maintenance as well as the sequence
of operations or steps that are needed.
The materials, replacement parts, and operations are all automatically
filled in the work order when you create it based on what kind of
maintenance the work order is being created for. If you need to change the
materials, replacement parts, or operations for a particular instance,
however, EZ Maintenance will allow you to do that.
To close the work order after the work has been finished, you just mark it
as closed and it is placed into the equipment maintenance history with all
the other closed equipment work orders.

If you want to create an unscheduled work order for an emergency maintenance
event such as an equipment breakdown, you just use the New
Unscheduled Work Order button. Using this button takes you to a
window like the one where you create a scheduled work order. However, you
have to choose the equipment which you're creating the work order for and
the kind of maintenance that needs to be done.

|
Previous
Section:
Viewing Maintenance
Due |
Next
Section:
Maintenance Due Report |
|
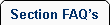 |
 |
1. |
Can EZ Maintenance produce actual calendars which show what maintenance or service is scheduled and what days it is to be performed? |
|
Yes, and you can even preset the calendars to include or exclude one or both weekend days. |
|
 |
 |
|
|
|